Blog
Transforming Smiles with Custom Aligners: How 3D Printing is Revolutionizing Dental Labs
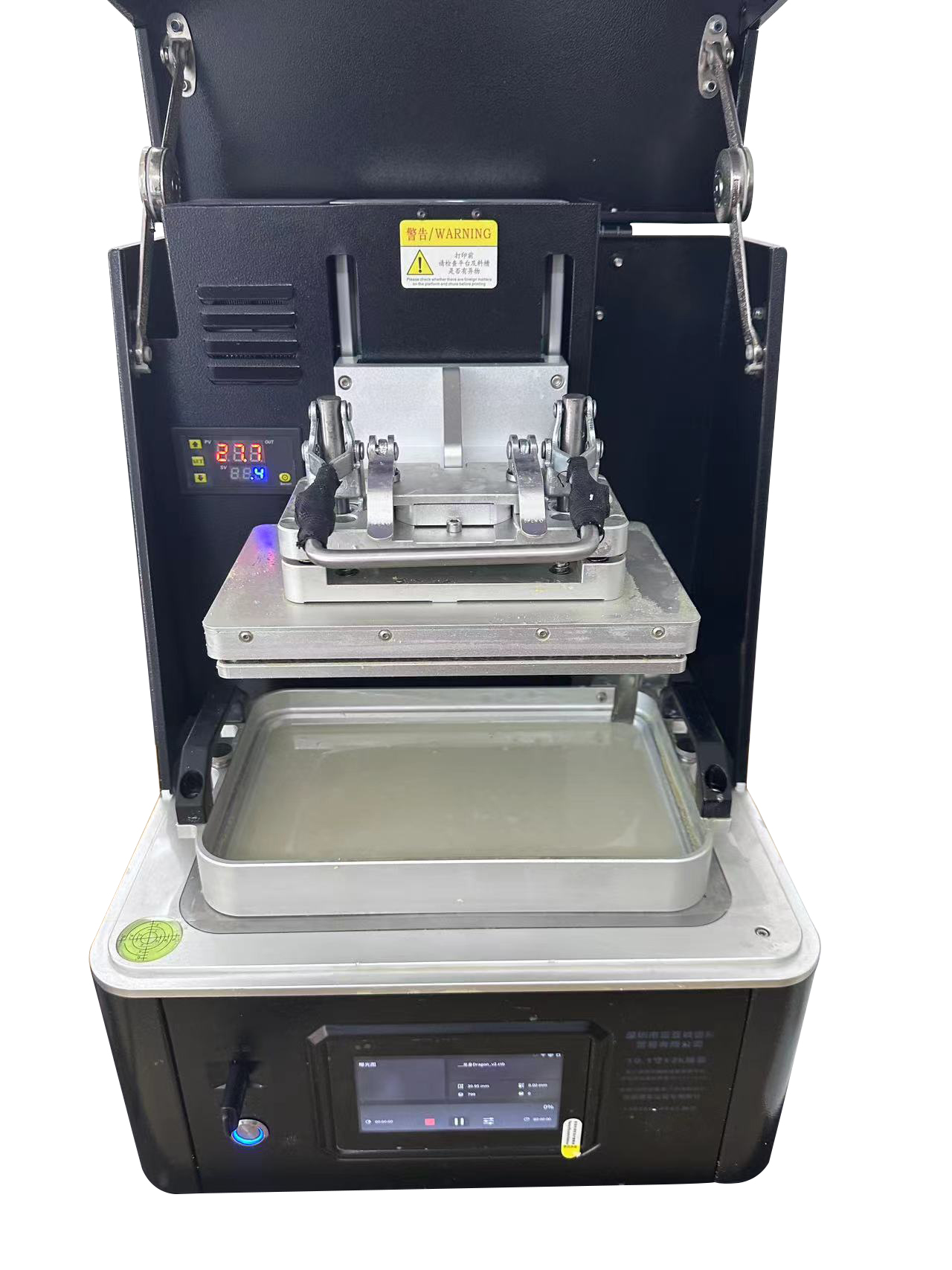
Advancements of 3D Printing in Orthodontics
3D printing has revolutionized the field of orthodontics, transforming the way dental labs fabricate aligners and other orthodontic appliances. This innovative technology has not only improved the quality and precision of aligners but has also streamlined the workflow, making it more efficient and cost-effective. In this blog post, we will explore the updated workflow procedure that showcases the seamless integration of 3D printing in fabricating 3D resin models and aligner production custom-made within dental labs.
The Initial Consultation and Data Capture
The journey towards a perfect smile begins with an initial consultation with the orthodontist. During this consultation, the orthodontist assesses the patient’s needs, considering factors such as the alignment of teeth, jaw position, and any other dental work required. The data capture phase is critical and can be achieved through two primary methods:
- Intraoral Scanner: Modern dental practices often use intraoral scanners to capture a digital impression of the patient’s teeth. This non-invasive method provides detailed digital models of the patient’s dental arches, which are then securely shared with the dental lab for further processing.
- Silicon Rubber Impression: In some cases, a silicon rubber impression may be taken. This physical impression is sent to the dental lab, where it is used to create digital models using a 3D desktop scanner. This step ensures that all necessary data is captured, even in cases where an intraoral scanner may not be feasible.
Specifying the Treatment Plan
Once the digital models are in hand, the orthodontist specifies the treatment plan. This includes the alignment goals, the desired outcome, and any other dental work that needs to be coordinated with the aligners. This information is crucial for the laboratory technicians, as it guides the design and fabrication process.
The Role of Laboratory Technicians
Laboratory technicians play a pivotal role in transforming the orthodontist’s vision into reality. With the help of 3D printing technology, they can create a series of precise, incremental models that are used to form clear plastic aligners. The necessary equipment and materials in a dental lab for this process include:
- 3D Printer: Used for creating a series of precise, incremental models.
- Desktop Scanner: Captures detailed digital impressions of the patient’s teeth.
- Curing Light: Essential for hardening the resin used in 3D printing models.
- Vacuum Thermoforming Equipment: Forms clear plastic aligners based on the 3D printed models.
- Resin: The material used in 3D printing for creating the incremental models.
- Aligner Material: The clear plastic sheets vacuum-formed over the 3D printed models.
- Support Structures: Necessary for maintaining the stability of complex 3D printed models during the printing process.
Their workflow, enhanced by 3D printing technology, is as follows:
Digital Modeling
Upon receiving the digital models or physical impression, technicians use specialized CAD software to create a virtual treatment plan. This involves designing each aligner in the series, considering the specific movements required for the patient’s teeth. The digital models allow for precise adjustments, ensuring that each aligner guides the teeth towards the desired position.
3D Printing
Once the digital models are ready, they are sent to a 3D printer, which creates a series of precise, incremental models. These models are printed using a resin material that is cured using a curing light. The 3D printed models serve as molds for the formation of aligners.
Vacuum Thermoforming
Once the 3D printed models are ready, they serve as molds for the formation of aligners. Vacuum thermoformer equipment is used to heat clear plastic vacuum former sheet material and form it over the 3D printed models. This process creates a perfect fit, tailored to the patient’s teeth.
Trimming and Finishing
After the aligners are formed, they are trimmed and finished to ensure a comfortable fit for the patient. Any excess material is removed, and the aligners are polished to achieve a smooth surface.
Quality Control
Before the aligners are delivered to the patient, they undergo a thorough quality control process. This involves checking the fit and accuracy of the aligners, as well as ensuring that they meet the treatment plan specifications.
The Synergy Between Orthodontists and Laboratory Technicians
The success of the aligner fabrication process hinges on the close collaboration between orthodontists and laboratory technicians. This partnership ensures that each aligner is not only precisely designed but also perfectly tailored to the patient’s needs. Regular communication throughout the process helps to address any adjustments or modifications required, ensuring the best possible outcome for the patient.
The Future of Orthodontics
As 3D printing technology continues to advance, we can expect further innovations in the field of orthodontics. The integration of smart materials that respond to the forces applied by the aligners could revolutionize treatment, making it more efficient and comfortable for patients. Additionally, the use of artificial intelligence in treatment planning could optimize the design of each aligner, further enhancing the effectiveness of orthodontic treatment.
Conclusion
The integration of 3D printing in dental labs has transformed the way aligners are fabricated, offering unparalleled precision, customization, and efficiency. The updated workflow procedure, from data capture to final production, showcases the seamless collaboration between orthodontists and laboratory technicians. This synergy, powered by cutting-edge technology, is not only improving patient outcomes but is also setting the stage for the future of orthodontics. As we move forward, the possibilities are endless, promising a world where perfect smiles are within everyone’s reach.